Molding metal is a fundamental process in manufacturing and craftsmanship, allowing raw materials to be transformed into everything from intricate designs to sturdy structures. Whether you’re a seasoned professional or just starting, understanding the different techniques and best practices is essential for success.
This guide will cover the most common metal molding methods, including casting, forging, and machining, along with tips to improve precision and efficiency. With the right knowledge, you’ll be able to create high-quality metal products that meet your project’s demands. Keep on reading!
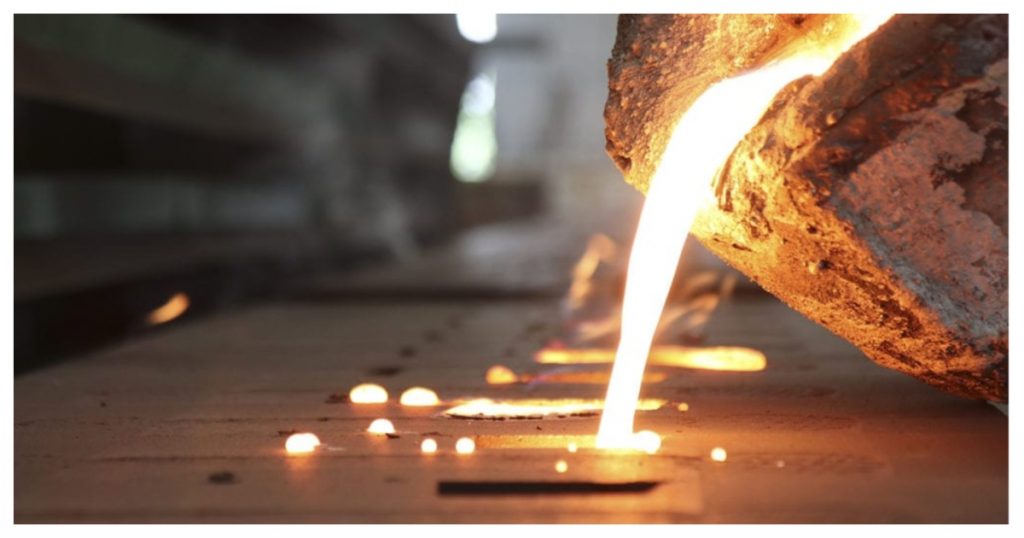
Techniques for Molding Metal
Know the different techniques to ensure efficient metal shaping. Here are some examples:
Sand Casting
Sand casting is a popular metal molding technique. It uses a mold made from sand to create metal parts. The process starts by packing sand around a pattern of the desired shape. The pattern is then removed, leaving a cavity.
Molten metal is poured into the cavity and allowed to cool. Once solidified, the sand mold is broken to release the metal piece. Sand casting is cost-effective and suitable for large parts. However, it may not be ideal for intricate designs.
Die Casting
Die casting uses high pressure to force molten metal into a mold cavity. The mold is made of steel and can produce precise, complex shapes. This method is efficient and produces high-quality parts with a smooth finish.
However, die casting is more expensive than sand casting. It is best used for high-volume production of small to medium-sized parts.
Investment Casting
Investment casting, also known as lost-wax casting, creates detailed and accurate metal parts. The process starts by creating a wax model of the desired shape. The model is coated with ceramic material to form a mold.
Once the ceramic hardens, the wax is melted and drained away. Molten metal is then poured into the ceramic mold. After cooling, the ceramic mold is broken to reveal the metal part.
Best Practices for Metal Molding
There are several practices to consider in metal molding. Here are a few examples:
Safety First
Safety should always be a priority when molding metal. Work in a well-ventilated area and wear protective gear, including gloves and goggles. Ensure all equipment is in good working condition to prevent accidents.
Handle molten metal with care to avoid burns and other injuries. Always follow safety guidelines and procedures. Proper training is crucial for anyone working with metal molding.
Quality Control
Quality control is essential for producing reliable metal parts. Inspect molds regularly for wear and tear. Even minor imperfections can affect the final product. Regular maintenance helps ensure consistent quality.
Use high-quality materials for both the metal and the molds. This reduces the risk of defects and improves the durability of the parts.
Efficient Workflow
An efficient workflow can save time and reduce costs. Plan each step of the molding process carefully. Organize your workspace to minimize unnecessary movements and delays.
Keep tools and materials within easy reach. Label and store them properly to avoid confusion. Regularly review and optimize your workflow to improve productivity. If you are interested in more advanced casting techniques, consider learning about this metal casting foundry in Texas.
Exploring Metal Forming Processes
Molding metal is a versatile and valuable skill. By understanding different techniques and following best practices, you can produce high-quality metal parts. Whether you’re a beginner or an experienced professional, there is always something new to learn.
Remember to prioritize safety, maintain quality control, and streamline your workflow. With practice and dedication, you can master the art of metal molding.