Sometimes, quantifying quality is a difficult task. Still, if you’re running a business, there’s no way to avoid it. You need to control quality to keep your company’s reputation, maintain your customers’ trust, and provide your company with a sustainable development plan.
Now, to do so, you need a quality control process. This systemic approach to quality control usually takes place in steps. With that in mind, here are the top six steps of a successful quality control process.
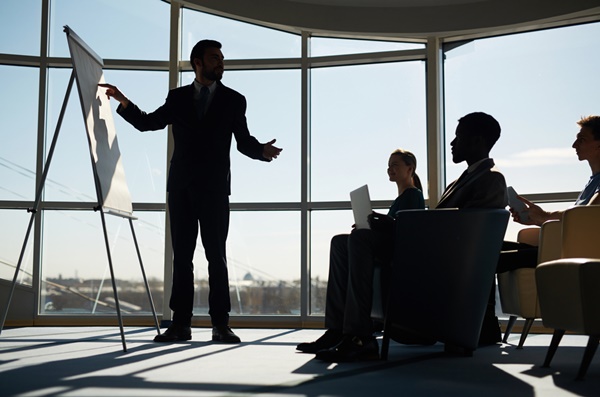
- Determine the requirements
You must first determine what you’re trying to accomplish in the quality control process. Do you want to pass the regulatory standards? Is your intention to increase the competitiveness of your product by meeting the quality of your prestigious competitors?
This is something you need to state in the outline.
Remember that every department has a quality of work that can be defined. Your customer service and sales are perfect examples of departments where, while difficult to define, the standards are relatively easy to set.
The big problem with evaluating anything is knowing what to do with the results. How do you know if they’re satisfactory? If they’re not satisfactory, how can you tell by how much they’re off? You need to resolve this before starting your quality control process.
- Create a checklist
The next thing you need to do to make this process systemic is to create a quality control checklist. This checklist should, at the very least, contain the following:
- Product requirements
- Packaging requirements
- On-site product tests and checks
- Defect classification
- Collaboration between the supplier and QC staff
The reason why you need a checklist is that your quality control process needs to be systemic. It needs to be the same so that the context doesn’t impact the results. Of course, this is impossible to achieve, but you must try.
With this checklist, you’ll have a pretty good idea of where the problem occurred and if there’s anything off about the product. This enables the most important aspect of your QC, which is the ability to fix a potential problem.
The simplest way to make a checklist is to download a QA/QC checklist template and edit it to fit your business process.
- Decide on the software you’ll use
There is much great software that you can use for quality control and risk management. Unfortunately, this can also be a problem since the paradox of choice hits hard. When faced with too many options, making a definitive choice is hard.
So, to make things easier, you might start by making your list of requirements. What features does your software need to have?
First, you want scalable software. You don’t want to switch when you meet an increased workload.
Next, you need to think about the industry-specific capabilities. While most tools are universal, you should probably look for one the rest of your industry uses.
Third, you need a tool that will allow you to customize the process. As we’ve mentioned, most of these platforms are generalist, so you need the ability to adjust them to your current industry and workflow.
Lastly, you need a reliable reporting and data storage system. Visibility of data and transparency are huge issues that you can’t ignore.
- Plan inspections
There are several layers to planning your quality control inspections.
First, you must determine the necessary frequency of tests or inspections. While these can be random, they should always occur in an X period. This way, you’re evenly spreading your inspections.
Next, you need to introduce the rule of tests and inspections on-demand. Sometimes, you’ll need to make an irregular inspection, and there must be a proper procedure to demand it. This way, you’ll integrate it into the system more effortlessly.
If there’s a special type of inspector that needs to become a part of the process, it’s important that you list them. Having a pre-set composition will contribute to the validity of the inspection.
In some scenarios, inspectors are the bottleneck of a work process. For instance, there are often points where the work cannot continue without approval. Make sure to identify these hold points to minimize the risk of downtime.
- Get feedback and evaluate it
Not all quality control is done by the in-house team. Inspectors are not the only source of information regarding the quality of your product. What do you do when you get a customer review or a comment on your social media post?
You need to have a system for evaluating this feedback.
Beyond doubt, some of these comments will just be outright malicious. Find the best video game, movie, or device on the planet, and you’ll find many negative comments. How do you tell between reasonable criticism and some outlandish claims?
The most effective way is to designate a part of your customer service to review this feedback. Then, you need a reporting system that will allow them to store it and send it higher up. This way, you can get the public sentiment.
- Correct mistakes
The most important thing about quality control is that it gives you enough insight to correct your mistakes. Without it, the insight would be useless.
First, you must report a mistake to someone with authority to kickstart the patching process. Second, you need to have a team assigned to solve the problem. Once this is done, it’s important that you conduct a new inspection and compare the new results with the previous ones.
Lastly, using this as a PR win might be a good idea. Your audience loves to be heard. Sometimes, this can even boost your team’s morale by showing them what a good job they’re doing.
Wrap up
In the end, even if you understand the objectives of your quality control, you need to make it systemic. Quality control is about controlling the quality of your product in a controlled environment. There are no other ways to compare results in a safe way. It’s also about making the process systemic so that you can actually analyze the results. Most importantly, you need to put a heavy emphasis on reporting.