If you’re involved in construction projects, you likely want to ensure that your projects are completed on time, within budget, and to the highest quality standards. But why is quality management so crucial in construction? Let’s explore this question.
Quality management is essential in construction projects because it helps ensure that the final product meets or exceeds the required standards, reduces the risk of defects and rework, and saves time and money – all of which are particularly important.
While this brief answer is accurate, there are additional factors to consider regarding the importance of quality management in the construction industry. Let’s dive deeper into how quality management can impact various aspects of your construction projects, from customer satisfaction to your company’s reputation.
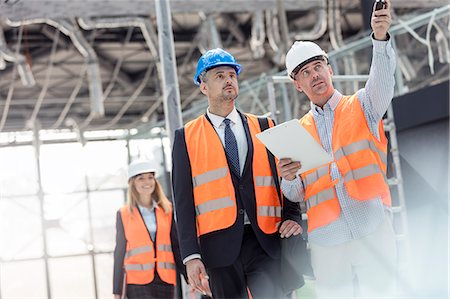
How Quality Management Affects Customer Satisfaction in the Construction Industry
Customer satisfaction is key to success in any construction project. By implementing effective quality management practices, construction companies can ensure that their projects meet or exceed customer expectations, even in the face of our challenging weather conditions. This includes delivering projects on time, within budget, and to the required quality standards. When customers are satisfied with the final product, they’re more likely to recommend the construction company to others and use their services again in the future.
Quality management also helps minimize the risk of disputes and legal issues arising from dissatisfied customers. By identifying and addressing potential quality issues early in the project, construction companies can avoid costly rework and delays that can lead to customer frustration.
The Impact of Poor Quality Management on Construction Costs
Poor quality management can significantly impact construction costs. When quality issues aren’t identified and addressed early in the project, they can lead to costly rework and delays. This can include having to tear out and replace substandard work, which is particularly expensive and time-consuming. In some cases, poor quality work may not be discovered until after the project is completed, leading to even more significant costs for repairs and remediation, especially if issues arise during our harsh winters.
Effective quality management practices, such as regular inspections and testing, can help identify quality issues early in the project when they’re less costly to fix. By investing in quality management upfront, construction companies can avoid the high costs associated with poor quality work and save money in the long run.
The Role of Quality Management in Protecting a Construction Company’s Reputation
A construction company’s reputation is one of its most valuable assets, especially in a close-knit states and areas. Poor quality work can quickly damage a company’s reputation, leading to lost business and difficulty in securing future projects. On the other hand, a reputation for delivering high-quality work can help a construction company stand out in our competitive market and attract new business.
Effective quality management practices can help protect a contractor’s reputation by ensuring that projects are completed to the highest standards, even in challenging conditions. This includes implementing rigorous quality control processes, investing in employee training and development, and fostering a culture of continuous improvement. By prioritizing quality management, Maine general contractors can build a strong reputation for delivering exceptional work and position themselves for long-term success.
In Maine’s tight-knit communities, word-of-mouth recommendations play a crucial role in a construction company’s success. Quality management becomes even more critical in this context, as it directly impacts customer experiences and the stories they share with others. By consistently delivering high-quality projects that withstand Maine’s diverse weather conditions – from harsh winters to humid summers – construction companies can cultivate positive testimonials and referrals. This is particularly important in smaller towns and rural areas, where reputation can make or break a business. Moreover, in an age of online reviews and social media, a company’s reputation can quickly spread beyond local circles. Quality management helps ensure that when residents search for reliable construction services, they find positive reviews and success stories that reflect a company’s commitment to excellence. This digital footprint, built on a foundation of quality work, can significantly enhance a construction company’s visibility and credibility.
The Importance of Quality Management in Ensuring Regulatory Compliance
Construction projects are subject to various regulations and standards, from state-specific building codes to environmental regulations protecting our natural resources. Failing to comply with these regulations can result in significant fines, legal issues, and reputational damage for construction companies. Quality management plays a crucial role in ensuring that construction projects meet all applicable regulations and standards.
Effective quality management practices include staying up-to-date with the latest regulatory requirements, incorporating these requirements into project plans and specifications, and regularly auditing projects to ensure compliance. By prioritizing regulatory compliance through quality management, construction companies can avoid costly penalties and legal issues while also demonstrating their commitment to responsible and ethical business practices.
How Quality Management Contributes to Sustainable Construction Practices
Sustainable construction practices are becoming increasingly important as companies look to reduce their environmental impact and meet the growing demand for eco-friendly buildings that can withstand any climate. Quality management can significantly promote sustainable construction practices by ensuring that projects are designed and built to minimize waste, conserve resources, and reduce energy consumption.
This can include implementing lean construction practices, which focus on minimizing waste and maximizing efficiency throughout the construction process. Quality management can also help ensure that sustainable materials and technologies, such as energy-efficient lighting and heating systems, low-flow plumbing fixtures, and locally sourced building materials, are used in construction projects. By prioritizing sustainability through quality management, construction companies can reduce their environmental impact, differentiate themselves in the market, and attract environmentally conscious clients.
Taking Action on Quality Management in Your Construction Projects
Now that you understand the importance of quality management in construction projects, it’s time to take action. Review your current quality management practices and identify areas for improvement. Develop a plan to implement these improvements, including employee training on building techniques, updating project plans and specifications to meet local requirements, and establishing regular quality audits to ensure ongoing compliance and success.